
Our Eco Pledge:
How Resolute Makes a Difference
​​
At Resolute, we're dedicated to minimising our environmental impact and providing sustainable solutions for textile printing. Our Eco Pledge reflects our commitment to reducing our carbon footprint and promoting environmentally friendly practices. We believe that every small action contributes to a larger change, and we strive to inspire others to join us on this journey towards a more sustainable future. Here's how Direct-to-Film (DTF) printing offers a significant advantage over traditional methods.




​Reduced Waste:
Unlike cut vinyl, large format printing, and white toner transfers, DTF uses minimal materials. The single film gets used efficiently, minimising waste compared to processes that generate leftover material like backing sheets and excess vinyl.
​Energy Efficiency:
​
DTF eliminates the need for multiple printing steps like pre-treatment and screen creation, reducing overall energy consumption. Water-based inks require less energy for curing compared to solvent-based inks used in some other methods.




Eco-Friendly Inks
DTF inks are water-based and odourless, free of harmful chemicals commonly found in plastisol inks used in screen printing. We offer OEKO-TEX, HAPS and REACH certified DTF consumables, ensuring responsible production and minimal environmental impact.

Sustainable Practices at Resolute:
We're actively developing DTF film made from recycled materials to further reduce our footprint. A universal cleaning solution reduces the number of cleaning products needed for our Resolute DTF systems by 50%. We're transitioning our company vehicles to electric models and offer free EV charging for visitors. We use recycled paper for internal printing, minimising paper waste.
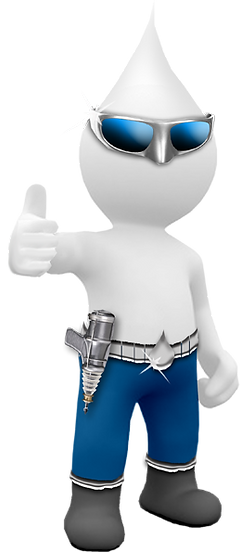
​​
DTF:
A Sustainable Choice
While the textile printing industry has room for improvement, DTF technology represents a significant leap forward in sustainability. By minimising waste, reducing energy consumption, and utilising eco-friendly materials, Resolute offers a responsible printing solution for businesses and environmentally conscious consumers.
​